2012
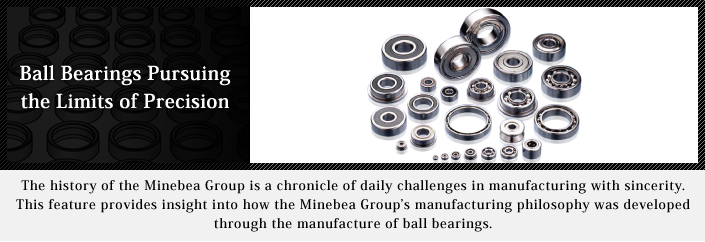
(Posted Oct. 2012)
An Endless Passion for High-quality Manufacturing
The most important performance measure in judging a ball bearing is the extent to which it reduces friction and facilitates smooth and easy rotation. Ball bearings may end up in aircraft, automobiles, precision machinery and many other end products, but no matter the application, it is important to maintain smoothness and minimize friction. Changes in the times brings diversification and complexity in end products and machine types along with new performance requirements for ball bearings, including miniaturization, higher rotation speeds, durability and duration, as well as noise reduction.
We have succeeded in responding to new requirements by carefully reviewing all of our product processes, from development and design to manufacture and inspection, and making steady, painstaking improvements. Since the structure of a ball bearing is very simple, however, improving the ball bearing has required enhancing the precision of the ball bearing components to their absolute limit. In order to do this, we decided to manufacture not only the critical inner and outer rings in-house, but the other components as well. Currently, Minebea also manufactures the cage, shield, and balls in-house. Additionally, to ensure the smooth rotation of the ball bearings, we have developed proprietary lubricants. We have also developed in-house a grinding machine which can be controlled to submicrometer (one-ten thousandth of a millimeter) precision, along with assembly equipment. To vertically integrate the business, we have enhanced the sophistication of the manufacturing capability and automated the manufacturing line. Today, nearly all the manufacturing equipment used in the grinding, polishing, and assembly processes were developed in-house.
While the design and quality of a product may be outstanding, if the price is too high, customers won't buy it. To improve cost-competitiveness, we evaluate the manufacturing processes from every angle, and strive to shorten the time from order to delivery while raising the yield. Another way we strive to beat the competition on price is to invest heavily in machine maintenance to ensure that our manufacturing equipment operates in optimal condition. This is another benefit of vertically integrating our business.
Column "Ball Bearing Manufacturing Processes"
The manufacture of a ball bearing can be divided into five major processes.
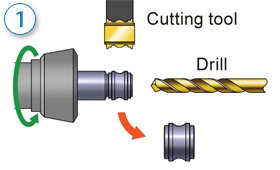
Cutting
Ring-shaped parts are cut from the raw material rods using drills and cutting tools.
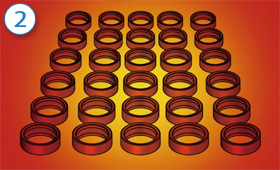
Heat Treatment
Process for hardening the parts in order to enhance their durability and long-life.
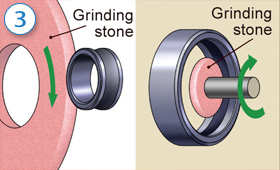
Grinding
A grinding stone is used to grind the surfaces of parts to the required dimensions and precision. Dimensions such as the outer and inner diameters and the width are ground to micrometer (one-thousandth of a millimeter) precision, as is the groove, a key internal structure formed between the inner and outer rings in which balls run.
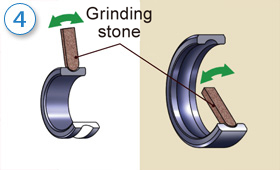
Honing
The groove between the outer and inner rings in which the balls run is honed to nanometer (one-thousandth of a micrometer) precision.
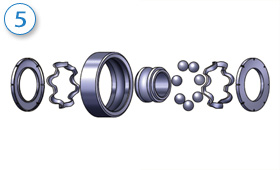
Assembly Process
The other ring, inner ring, balls and cage are assembled, oil or grease is applied to aid smooth rotation, and covered by a shield. This is the process where exactly the right parts are assembled to meet the customer's specific requirements.